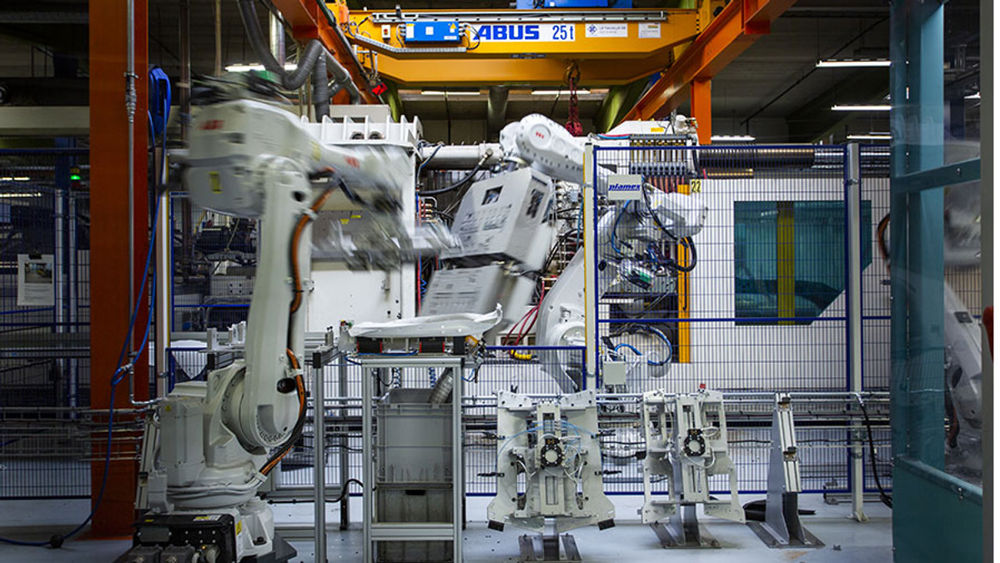
Why KB Components went for Monitor ERP
A standardized, cost-efficient system tailor-made for manufacturing companies. For Swedish manufacturer KB Components, changing to the Monitor ERP system created a world of new opportunities, both now and in the future. “The system can be continually updated with new, flexible functions and modules,” said Daniel Harrysson, ERP project manager at KB Components.
Swedish firm KB Components was founded in 1947, with the goal to drive the development of the plastics injury. Just over 70 years on, it has become one of Scandinavia's biggest players, delivering innovative plastics and components solutions to a host of world-leading manufacturers in the medical technology, furniture, chrome plating, industrial technology and lighting sectors. KB Components is also subcontracted by some of the world’s biggest car manufacturers.
Headquartered in Örkelljunga, its operations are based all around the world. With over 800 employees, the company has a total of six production units across three continents.
Manufacturing forms the core of KB Components’ operations, and this requires a system which supports its highly automated production workflow, from raw material to final product. As part of this process, in February this year KB installed the Swedish ERP system Monitor ERP, which meets the unique needs of manufacturing companies.
Around 5,000 companies around the world currently optimize their operations with the help of Monitor, the system which is now in its fifth generation, 40 years after it was first launched. One of the system’s benefits is that it’s standardized, which means there’s no need to hire consultants when it’s time to produce new reports, lists, labels, and other useful presentations. This also boosts cost-efficiency.
Other systems previously used by KB Components were more expensive to update and more difficult to develop compared to Monitor. This limited its options.
“The system can be continually updated with new, flexible functions and modules,” said Daniel Harrysson, ERP project manager at KB Components.
It allows us to automatically create and release purchase orders to ensure we have the right material in the right place, at the right time. This gives us peace of mind throughout the production chain.
According to Harryson, manufacturers like KB Components have many requirements when it comes to an ERP system. In addition to supporting and keeping track of key business processes and presenting real-time data for operational planning, it also provides effective assistance to users in their day-to-day work.
The ability to switch between different companies and languages was another reason the company chose Monitor ERP.
“With operations based all over the globe, it was important to choose a solution that enables us to use the same ERP system in all our companies worldwide."
The system is currently used in practically every department and unit within the company, from production to administration.
“We use the system in order to add new suppliers, for example, and we can also create and release purchase orders to ensure we have the right material in the right place, at the right time. This gives us peace of mind throughout the production chain."
KB Components also uses the system for time recording, authorizing supplier invoices, releasing customer orders, invoicing customers, and generating sales forecasts.
“The requirements planning function uses forecasts to determine what we need to manufacture, and when we must do so to deliver on time. We can warmly recommend Monitor. We’ve always enjoyed an excellent relationship, both during implementation and now, after going live,” added Harrysson.
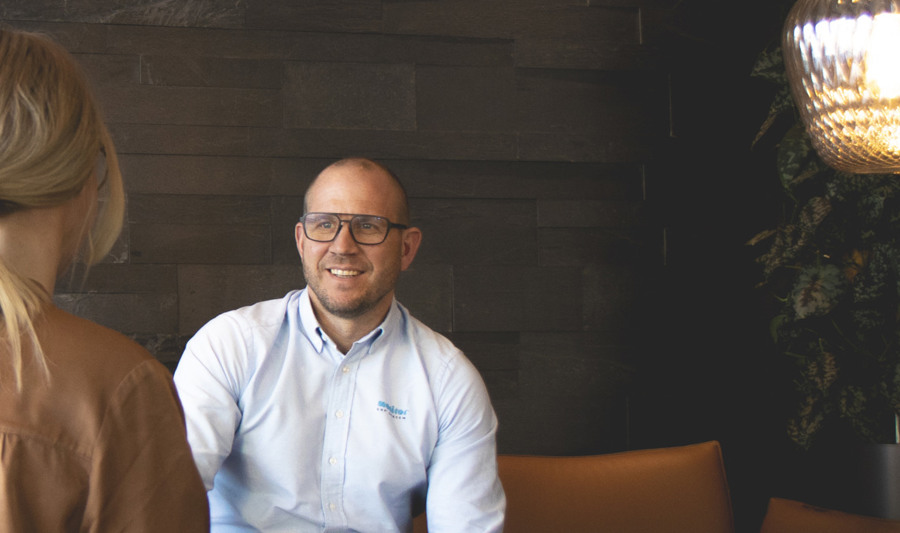