BEFORM streamlines operations through Monitor ERP and Machine Integration (MI)
After a period of pandemic, rising transportation costs, and general supply issues from abroad, more and more customers are seeking closer geographic proximity to their suppliers. This creates new opportunities for the plastic manufacturer BEFORM.
At BEFORM Hønefoss, production manager Håkon Ekre sits in front of several screens displaying numbers and tables. From here he can monitor production of the company’s 36 injection molding machines in real-time – whether the machines are running, production speed, the number of units produced, the number remaining, if the current order’s production time is being met, and so forth.
This is made possible because BEFORM Hønefoss now has Machine Integration (MI) as part of its Monitor ERP software. MI is a tool which integrates the company’s machines with Monitor ERP for automatic reporting of factors such as time usage, production numbers, and downtime.
“In the past, we were dependent on the machine operator manually reporting production,” Ekre explains. “Now it’s done automatically, providing a comprehensive real-time view of the entire production process.”
Being able to see live what items we have in the system at all times gives us better control over everything – and fewer gray hairs!
Better control
The Hønefoss factory employs 26 people, 12 of whom are directly involved in production, serving customers such as OSO (water heaters), Kongsberg Automotive (automotive parts), Calpro (pharmaceutical parts), and Nippon (gas mask parts), to name a few. The main focus is on series production, with the number of units per order varying from a few thousand to nearly a million.
Production manager Ekre has been a strong advocate for integrating Machine Integration as part of the company’s ERP system, emphasizing the ability to customize the MI module in Monitor to suit their needs.
“I’m probably more of a nerd than average when it comes to this stuff,” he admits. “But experience shows that we gain much better control over production. Being able to see live what items we have in the system at any given time also has positive effects for other employees in the company, such as planners, buyers, and warehouse workers.”
Being prepared
The implementation of Machine Integration in Monitor began after the summer of 2022, and the option was fully rolled out during the fall.
“It’s been a very manageable process,” says Ekre. “We’ve handled some teething problems together with Monitor, and now we’re nearing the goal.”
The production manager believes it’s important to be well-prepared, and considers a 3-4 month adjustment period to be realistic.
So what has been the greatest benefit so far?
“Being able to see, live, what items we have in the system at all times. This gives us better control over everything – and fewer gray hairs!”
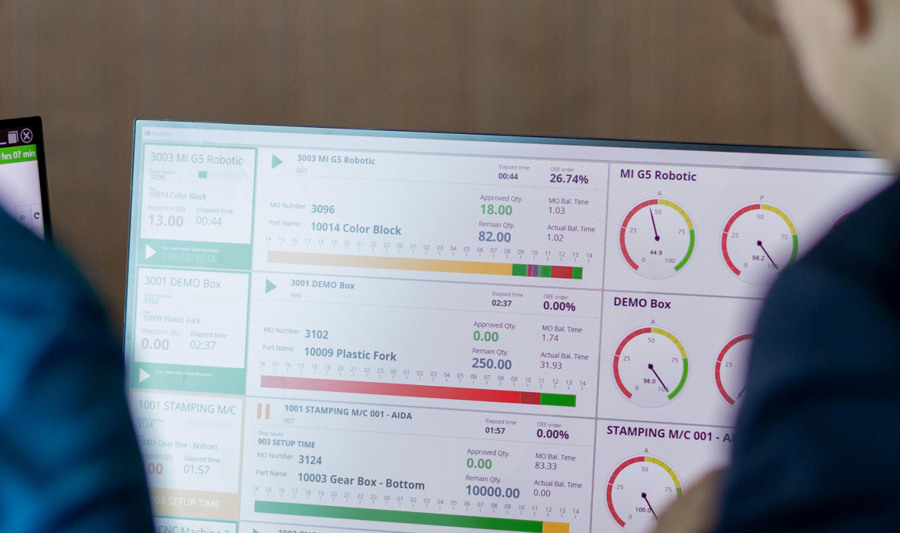