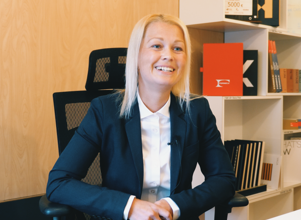
"No other ERP system could do this" - Why Plaat Detail chose Monitor ERP
When Estonian manufacturer Plaat Detail set out to digitalize their entire production, they didn't just need any old ERP, they needed one built for real-time control, automation, and sustainability. No other ERP system in Estonia could deliver what they were looking for. That’s why they chose Monitor ERP.
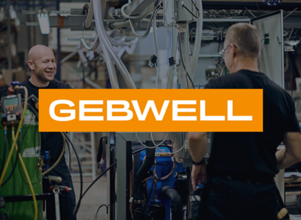
Gebwell Oy switched to Monitor ERP in record time
The ERP system was upgraded to support the company's growth, internationalisation and business process development.
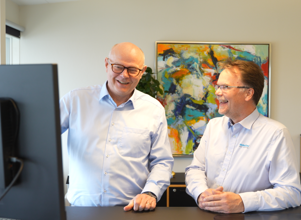
Focus on efficiency and trust: Lind Jensen Maskinfabrik and three years with Monitor ERP
For more than 60 years, Lind Jensen Maskinfabrik has delivered quality solutions to a wide range of industries. With more than 100,000 different parts to keep track of, a good ERP system was a necessity. Three years ago, the company decided to switch to Monitor ERP - a decision that has strengthened operations, overview and collaboration across national borders.
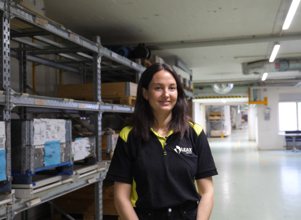
“I don’t understand how we managed without it!” – LEAX Skaraborg boosts efficiency with Advanced stock management
When LEAX Skaraborg chose to implement Advanced stock management, their daily workflow improved significantly. From manual and time-consuming to efficient and well-structured.
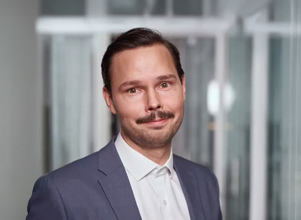
Harald Pihl chooses Monitor ERP as their secure, efficient, and future-proof cloud solution
Harald Pihl, an international, family-owned company with expertise in special alloys and metals, was looking for a cloud-based ERP system. They chose Monitor ERP, whose cloud solution offers security, flexibility, and reliability, as well as easy access for their employees around the world. Operating the system on-site would have required scaling up the IT department and posed more risk, making the cloud solution the most efficient and secure option.
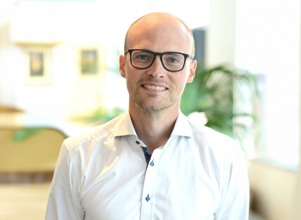
Bank integration helps ELMAB simplify their payment flows
For ELMAB, a leading Swedish manufacturer of hydraulic cylinders and components, Monitor ERP’s Bank integration has been a significant success factor. Bank integration optimizes the finance department’s day-to-day work by automating payment flows, reducing manual input, and minimizing the risk of errors.
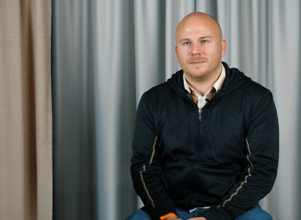
Aura Light reduces their climate footprint thanks to Sustainability by Monitor
With the help of Sustainability by Monitor, Aura Light has changed the material used in their Helags industrial lighting, thereby reducing their carbon footprint. Through changing the material used in production, the carbon emissions have been reduced by over 45%, resulting in a total reduction of the product’s carbon footprint by 10%.
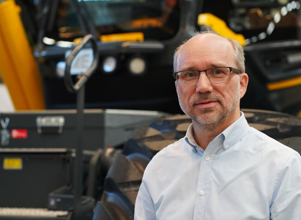
From manual to automated – Eco Log optimizes their processes with PDM integration
For Eco Log, a leading manufacturer of forestry machinery, the pursuit of efficiency and high-quality data is what led them to implementing PDM integration. Thanks to PDM integration, Eco Log has successfully been able to automate the transfer of data between their product data management (PDM) and Monitor ERP, which has eliminated duplication of work and reduced the risk of errors.
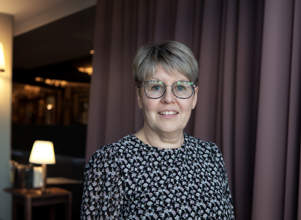
From paper to app – Olofsfors optimizes their expense management with Monitor Expense
Olofsfors, a company that specializes in manufacturing high-quality steel products, is now able to manage their expenses both easier and quicker with the help of Monitor Expense. The digital solution reduces their paperwork, saves them time, and simplifies processes for both employees and the finance department.
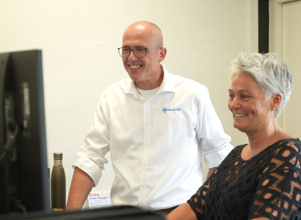
Monitor ERP Helps Bjerrum Nielsen Boost Productivity
Almost three years ago, the Danish production company Bjerrum Nielsen took a significant step by replacing their old ERP system, C5, with Monitor ERP. The implementation was managed by Monitor, and it has proven to be a good decision for the company, which now sees major improvements in their operations.

Skotte AB chooses Monitor ERP due to its sustainability feature
Monitor’s complete ERP system and sustainability function were two determining factors when it came to Skotte AB’s choosing Monitor as their new ERP system. Skotte AB offer a wide range of products that are optimized for their customers across multiple industries, from product owners to contract manufacturers. They focus on finding the best manufacturing methods and processes to maximize efficiency and ensure products of the highest quality.
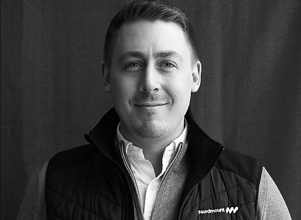
Nordmount’s success with Monitor ERP sets a new standard in the solar panel industry
The Swedish company, Nordmount, has established itself as a leader within the design of solar panel mounting systems. Produced in Sweden with a focus on simple, efficient, safe solutions, they have gained the trust of installers and raised the standard for rooftop installations. Nordmount’s commitment to quality also provides excellent results for those who live and work under their installations.
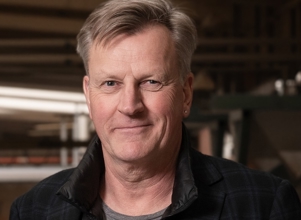
Ifö Electric chooses Monitor ERP due to its cost-effectiveness, good reputation, and extensive functionality
After careful evaluation, Ifö Electric, a manufacturer of Diazed fuse links, distribution cabinets and lighting, as well as all types of low and high voltage fuse links and accessories, has chosen Monitor ERP as their new ERP system. Monitor ERP’s cost effectiveness, good reputation, and functionality played a crucial role in the decision.
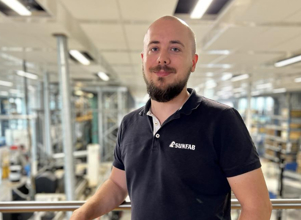
Sunfab has taken a strategic step forward by upgrading to G5
After using Monitor ERP for over 30 years, Sunfab, which is based in Hudiksvall, Sweden, has upgraded from G4 to G5. David Olsson, project manager for G5 at Sunfab, shares their journey with us and tells us about the possibilities that the upgrade has brought to the company.
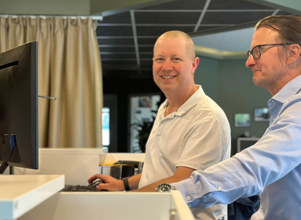
Monitor ERP’s the Agent makes National’s administrative procedures more effective
For National, a company specialized in the manufacturing of high-quality rubber, plastic and fiber products, Monitor ERP’s option, the Agent, is the obvious choice. Administrative procedures have been automated, which has led to an increase in productivity.
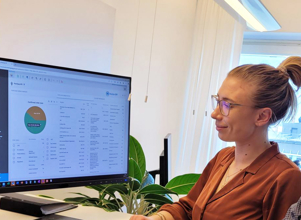
Koenigsegg creates dashboards and KPIs with Monitor BI
Koenigsegg sees the many advantages of Monitor BI and regards it as a powerful tool that can quickly give them an overview of their data, while also being able to provide detailed reviews in the same dashboard. Monitor BI’s ability to present easily understandable data to the whole organization and self-instructional dashboards are what Koenigsegg considers to be the most significant advantages.
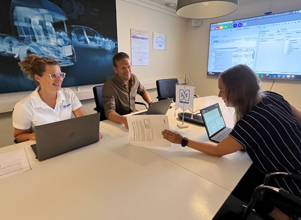
Nitator works greener with Sustainability by Monitor
To take their sustainability efforts a step further, the company Nitator, a prominent player in the automotive industry and a comprehensive supplier of sheet metal components, has begun using Monitor ERP's environmental feature – Sustainability by Monitor. Sustainability by Monitor is an environmental tool which helps companies to accurately measure their environmental impact and implement sustainability measures.
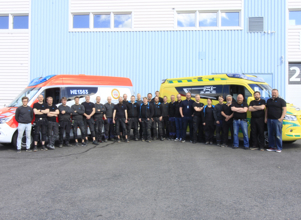
How Monitor ERP helps J5L-Production Oy with their sustainability
To strengthen its position in sustainability and the rapidly evolving business world, the Finnish company J5L-Production Oy, which manufactures specialist vehicles, realized it needed a new, powerful ERP system. After careful consideration they chose Monitor ERP.
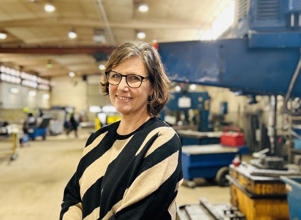
Effective time recording – a necessity for Borins AB
For the Swedish company Borins AB, which is known for its broad range of high-quality products and services, Monitor’s TimeCard plays an essential role. By using TimeCard, Borins AB’s employees can easily record their working hours directly on specific work orders, which means that they no longer need to separately record different working tasks.
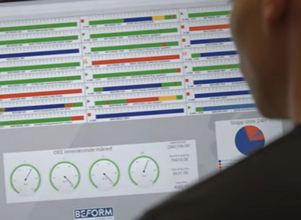
BEFORM streamlines operations through Monitor ERP and Machine Integration (MI)
After a period of pandemic, rising transportation costs, and general supply issues from abroad, more and more customers are seeking closer geographic proximity to their suppliers. This creates new opportunities for the plastic manufacturer BEFORM.
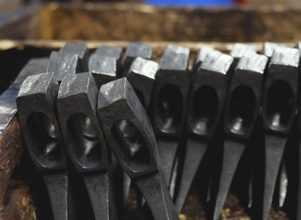
Gränsfors Bruk now runs Monitor G5 – “The upgrade was seamless”
Gränsfors Bruk now runs Monitor G5 – “The upgrade was seamless”
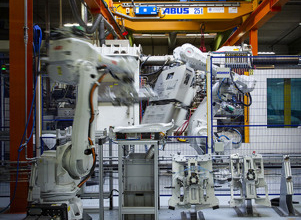
Why KB Components went for Monitor ERP
For Swedish manufacturer KB Components, changing to Monitor ERP means new opportunities, both now and in the future.
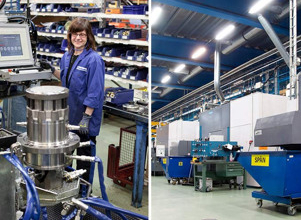
Monitor G5 the logical choice for Indexator
The group includes four other companies which have all run Monitor for several years, so when it was time to change ERP system, the choice was simple.
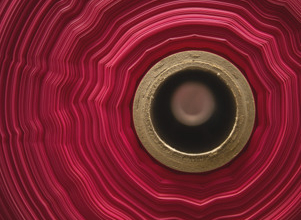
Alfapac chose Monitor ERP to pinpoint production
According to Financial Manager Marcus Kindevåg, Monitor is clearly a system designed for manufacturing companies. "There’s a depth to the system which we can utilize when following up our production, and in reports.”
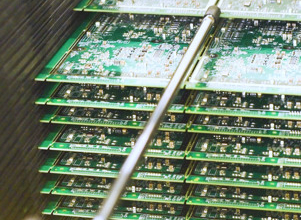
Monitor improves Darekon's supply chain management
Join us on our tour of Darekon’s facilities, get a glimpse of their day-to-day work and see how Monitor ERP makes life easier for Darekon’s employees.
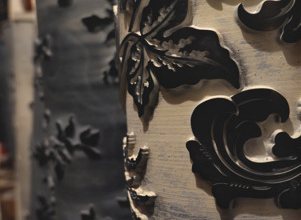
Duro steps up production with Monitor G5
To handle a larger process flow, we needed an ERP system that was efficient, and wouldn’t cost administrative time. And we chose Monitor ERP.
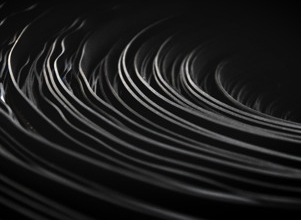
More efficient manufacturing with Monitor G5: “A real boost”
National Halmstad needed a more standardized ERP system which could help it achieve its goal – a digitalized, effective process flow throughout the factory. So it chose Monitor G5.
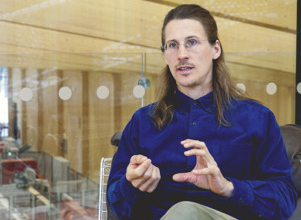
Becoming the world’s greenest furniture company – with Monitor ERP
The Norwegian company Vestre has gone through a lot over its 75 years. Its current focus is to be “the world’s most environmentally friendly furniture manufacturer”.
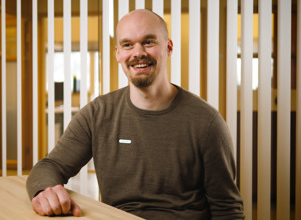
Project-based manufacturing with Monitor G5
C&D Snickeri is a manufacturer of wood interiors. Each new customer means a new project with new products. “It's important for us that the ERP system can manage the rapid flow of parts and products that pass through our doors,” explains site manager Emil Carlson.
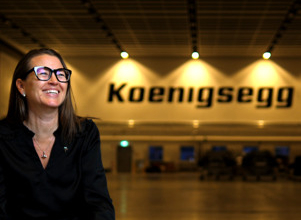
The key to a successful upgrade
With new car models and new factories in the pipeline, Koenigsegg needed a new ERP system. An upgrade is a major project. But Koenigsegg swiftly moved through the gears.
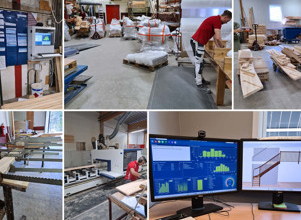
Monitor ERP – a savior in times of need for Olssons Trappor
After a year of pandemic and uncertainty, co-owner Kim Olsson talks about the company’s rewarding journey with Monitor.