Extensive functionality
To make the system as accessible and easy to use as possible we’ve divided its functionality across modules: Manufacturing, Purchase, Sales, Stock, Time recording and Accounting. Together they form an extensive support system for the majority of processes and workflows within a manufacturing company.
How does Monitor ERP work in different industries?
We’re experts in most areas of manufacturing, whatever field you work in. Plastics, metal, wood, automotive, electronics, food, project-managed manufacturing, machine manufacturing ... you name it!
Measure your products' climate footprint with Monitor ERP
Sustainability by Monitor
In 2026, all small and mid-sized enterprises in the EU will be required to file sustainability reports according to the EU's CSRD directive and ESRS standard. Our Sustainability by Monitor functionality helps you to measure your carbon footprint, evaluate the data and adopt strategic measures to cut emissions and consumption of resources.
Why use Sustainability by Monitor?
✔ Calculate carbon footprint
✔ Adopt strategic measures
✔ Compatible with the ESRS
✔ Included in Monitor ERP as standard
Smarter decisions with clear visualizations
MONITOR BI
Discover the power of Monitor BI – a function that converts your company’s data into valuable insights. Monitor BI gives you the tools you need to easily and effectively analyze data, create compelling visualizations, and make smarter decisions.
Why choose Monitor BI:
- Gathers data in one place
- Create dashboards and KPIs
- Web-based
- Standard in Monitor ERP
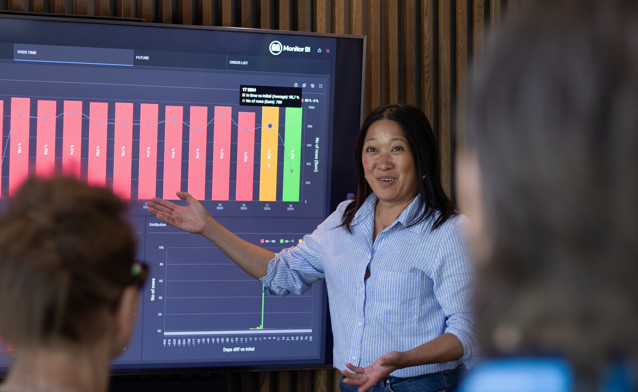
Are there different versions of Monitor ERP?
Monitor ERP is our ERP system, provided by Monitor ERP System AB. We normally say “Monitor” in both cases. And if we ever call our ERP system “Monitor G5” it’s just to clarify that we’re talking about the fifth and latest generation. Crystal clear?
If you already run Monitor ERP but have not yet upgraded to G5, don’t hesitate! Read more about G5, and how the upgrade process works.
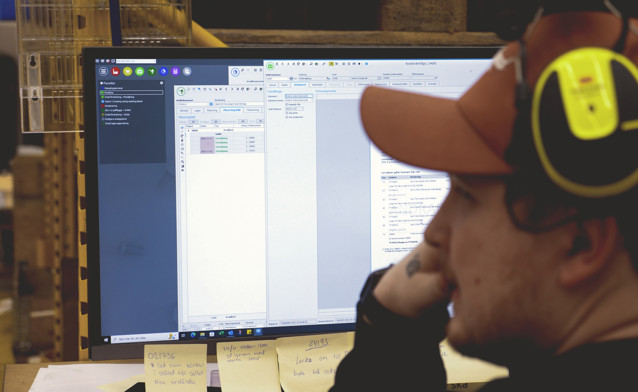