One complete ERP system to support growth
SP stainless realized its numerous legacy programs had become a barrier to continuous organic growth. This slowed down workflows and disrupted production efficiency. To revamp its operational efficiency it realized the need to digitalize operations and optimize processes and workflows. The journey to find a complete ERP system to manage operations was critical to its future success and future growth ambitions.
SP stainless Oy is a contract manufacturer based in Finland. Founded in 1989, it provides piping, pipe fittings, and equipment to meet industry needs. Since the start SP stainless has grown organically, both through mergers and company reorganizations. It currently has two modern production facilities, one located in Siilinjärvi, Toivala, and another in Savonlinna, employing a total of 50 metalwork professionals.
We decided to visit SP stainless's production plant in Siilinjärvi, Toivala, to see how the team uses and benefits from the Monitor G5 system when managing its daily work.
A complete ERP system to support growth
Arto Koljonen, CEO of SP stainless Oy, outlines how, due to the company’s growth ambitions, it was time to find a new ERP system that would enable them to manage their business growth profitably.
"The company's growth has been stable, with no big leaps, and our turnover is now around EUR 7 million. In order to manage this growth we arrived at the need for a new system, which supports our sales, and above all, helps manage our production,” he explains.
Over the years, SP stainless had amassed several legacy systems through mergers and acquisitions. Koljonen says their intention was to get rid of these and find one complete ERP system that would support their growth process. The new ERP system would take their manufacturing operations to the next level.
“The goal was to find a system which included as many functions as possible, that is, to weed out unnecessary programs. The objective was also to improve the sales process and manage purchases in a timely manner, improving production control as well as traceability.”
We don't spend time searching and investigating in vain. The information is where it should be.
Hannele Ranta, Development Engineer at SP stainless, explains that the company chose Monitor ERP due to the system’s industry-specific basic functions, and because it’s a complete, cost-efficient system with processes adapted to support manufacturing.
“We chose Monitor purely because of the clarity of its processes. Customer management can be handled relatively easily in Monitor G5, and this was the most logical and comprehensive system. So there was no need for us to begin creating adaptations for the system’s core functions. We use it with its basic functionality. This is the best solution for us, and the most cost-efficient approach when acquiring a new ERP system,” Hannele says.
Less waste with traceability
SP stainless has invested significantly in the development of its business in order to meet its customers’ requirements. Arto Koljonen sees that, in order to be regarded as a quality manufacturer in Finland, and internationally, they must constantly invest in the development and quality of their operations. One important development phase relating to the Monitor G5 ERP system was implementing a new advanced traceability system to manage the quality of production on all levels.
With the introduction of the traceability system in the company, SP stainless has succeeded in improving its internal efficiency, stock management, and generating less waste. Employees now know easily where to find the products and materials at the production sites. Monitor G5 has made it easier for production workers to have a good workflow, enabling them to find the right materials, at the right time, for handling and processing, and also deliver products to customers as promised. Arto Koljonen explains that, after some initial issues, Monitor G5's advanced traceability system has become the most appreciated feature.
“In the beginning, there was resistance, as it took time to mark this. But after we’ve now been working with this a while, we’ve realized that it is one of the best features Monitor G5 has given us.”
Hannele Ranta explains that because information is now up-to-date in the system, production planning challenges are much easier and faster to resolve than before.
“This helps us to find out if there are any challenges in production, so we can locate the right worker, and know to ask the right person, so time is not wasted searching and clarifying. This is definitely one of the biggest benefits. Information is where it is supposed to be,” she adds.
Seamless cooperation is the backbone of the ERP project’s success
Arto Koljonen reflects that cooperation with Monitor has been seamless, and that the ERP project stayed on schedule – and costs remained below budget. Hannele Ranta shares Koljonen's view, noting that cooperation with Monitor has been fruitful throughout the whole ERP project and beyond.
“Our project started in 2020, and in 2021 we started to begin implementing the ERP system. A long investigation phase took place whereby Monitor’s salesperson was supportive and active from the start, and was able to answer most of our questions and find out what was important to us. The same Monitor consultant also continued, and used a good model when the implementation began. It was easy to cooperate, and it’s still easy to work and communicate with Monitor if there are any issues,” Hannele says.
She recommends the Monitor G5 system to all manufacturing companies.
“Monitor G5 can be recommended strongly to all manufacturing companies where there is production and warehouse, because this is a complete system which also has an accounting module. The basic functions are included from the start, and easy to find. I don't really know to whom I wouldn’t recommend the system. At least it's worth a look. And if you choose Monitor G5, you’ll get a system with a lot of functionality and a cost-efficient solution."
Arto Koljonen also recommends Monitor G5 to companies in the manufacturing industry. He also reflects that the Monitor G5 system has significantly speeded up his own work. Koljonen explains that with the ERP system, they have succeeded in streamlining their activities and operations and thereby achieved their business goals.
“The sales process has been streamlined and, above all, purchases and warehouse management are in a good place. Production is now under control and at a reasonable level, and now the system shows us where we are heading with our work,” he says.
Summary
Monitor G5’s out-of-the-box manufacturing industry software proved to be the best solution. It enabled SP stainless to break free from its large stack of legacy issues and manage its growing business. Monitor G5’s manufacturing industry-specific system was SP stainless’ ultimate choice. This new ERP system allowed SP stainless to implement a new traceability system to manage quality and material flows, while transparency of the system helped to improve internal workflows, breaking silos and aligning business processes into one complete ERP system. This enabled SP stainless to manage and monitor its production levels, keep track of purchases, stock levels and material flows to fully support customers’ growing demand for high quality products.
Looking to expand and manage your manufacturing company more profitably? Get in touch with us to learn more about how you can benefit from our manufacturing expertise, and how Monitor G5 can benefit your business.
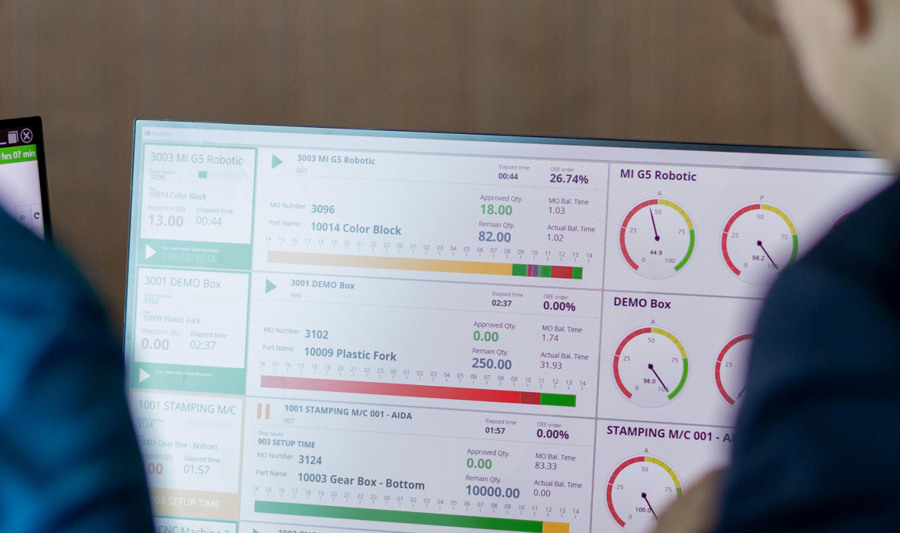